Net Zero and Wet Gas Metering
Richard Steven, Principal Measurement Consultant
The drive to net zero has many technical challenges. Thankfully the engineering technology of the existing energy sector is well placed to solve various net zero technical requirements.
One such challenge is the control of net zero systems such as geothermal steam power production, wet hydrogen extraction from cavern storage and carbon capture and storage (CC&S). Operators of each of these net zero endeavours encounter wet gas flows, i.e. gas flows with entrained liquids. Wet gas flow is notoriously challenging to meter.
Geothermal steam wells naturally produce saturated steam with qualities < 100%, i.e. the flow is a mix of steam and water. Control of the system, i.e. control of the wet steam production flow, is achieved via valve settings, but only if the flow conditions are quantifiable. Too low a quality means too low an energy (enthalpy) supply. Too high a quality can cause excess scaling of pipe. Accurate metering of the wet steam is desirable.
Hydrogen, produced by water electrolysis powered by renewable (or conventional) energy sources, is often stored in salt caverns. The hydrogen extraction process tends to produce a hydrogen with entrained water flow, i.e. a wet gas flow.
Carbon dioxide (CO2) gas captured from fossil fuel power stations is transported to storage at thermodynamic conditions convenient for efficient large scale processing. Rather inconveniently these conditions are close to the CO2 gas / liquid phase boundary. Hence, wet gas monitoring and even wet gas metering is important to CC&S.
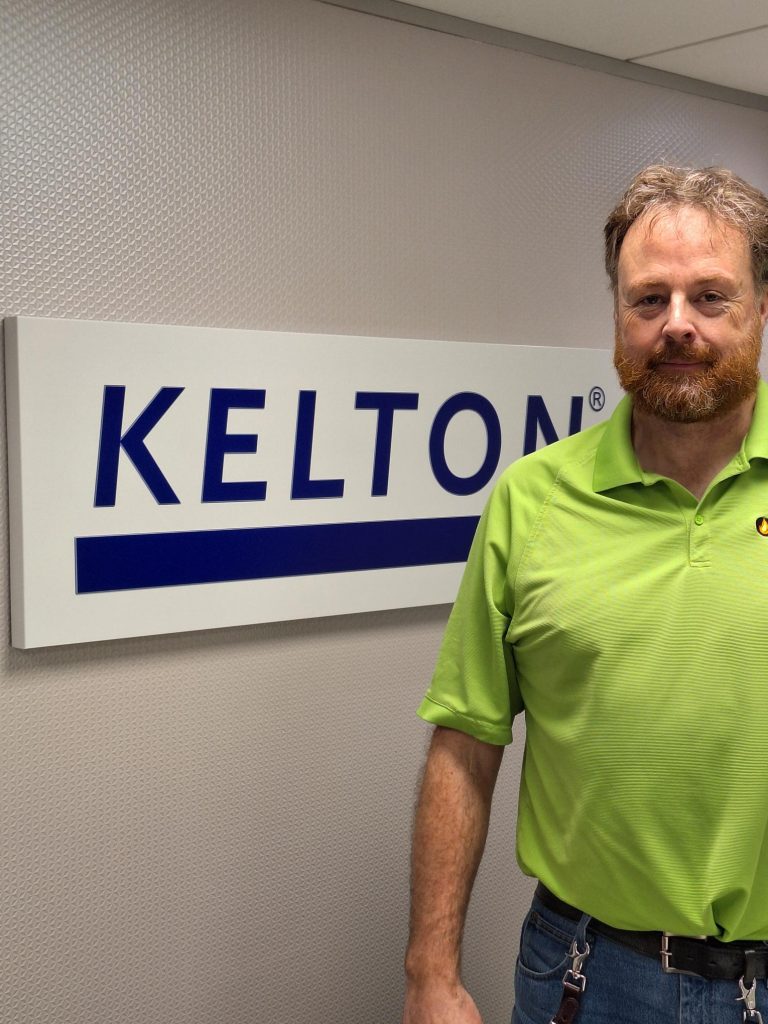
Wet Gas Metering and the Hydrocarbon Industry
Wet gas metering is an order of magnitude more challenging than single phase flow metering. Thankfully, these net zero wet gas flow metering technical challenges do not have to be met with virgin technologies. The hydrocarbon production industry has long been developing various wet gas metering methods, and these are transferable to these new net zero industries.
The formal ISO definition of wet gas flow is rather abstract, but a rule of thumb is wet gas flow can be considered a Gas Volume Fraction (GVF) > 95%, i.e. a liquid volume flow of ≤ 5%. With the density difference between gas and liquid, in mass terms this can mean as much liquid as gas. Such quantities of liquid adversely affect single-phase gas meters, causing significant positive biases on gas flowrate prediction while not metering the liquid flowrate. This has long been a problem for the hydrocarbon production industry. Natural gas wells produce wet gas, i.e. natural gas entrained with water and liquid hydrocarbons. After initial processing single-phase natural gas can have condensation of heavier components as the conditions change. As such wet natural gas metering has been researched and developed for several decades.
Wet gas flows have been prevalent in industry since the industrial revolution. The power sector, driven by the advent of nuclear power and the need to accurately meter saturated wet steam flow, started wet gas metering research in the 1950s. However, by the 1980’s this power sector wet gas metering R&D was waning while the natural gas production industry’s R&D on the subject was increasing. Initially adopting the power sector’s published wet gas meter methodologies the hydrocarbon production industry soon further developed them as well as diversifying to various different sophisticated wet gas meter technologies.
Wet gas metering remains important to the hydrocarbon production industry. With the modern tendency for shared processing plants it is necessary to meter the wet gas flows from individual wells before commingling with 3rd party flows upstream of the communal processing plant. The process plant’s natural gas and liquid hydrocarbon need to be allocated for profit, and any produced water needs to be allocated for disposal cost billing. Reservoir engineers prefer individual well wet gas flow data to aid in well management and maximize the return on their investment. Good measurement allows the reservoir engineer to maximize the well’s production before artificial lift expenses have to be incurred. Furthermore, as a wells age, or marginal wells are brought on line, they tend to introduce wet gas flows into the system that require metering. Today wet gas meters are being used for monitoring, allocation and custody transfer applications subsea, topside, and onshore, from high end production to marginal fields.
The Complexity of the Wet Gas Metering Challenge
Wet gas flow is a very adverse flow condition to all single phase gas meter designs. If they manage to output a gas flowrate prediction, it will most probably have a liquid induced positive bias. This gas flowrate prediction positive bias is called the ‘over-reading’.
Turbine meters, and early model ultrasonic and Coriolis meters failed in wet gas service, or at least outputted nonsensical values. Modern vortex, Coriolis, and some chordal path ultrasonic meters are more robust and can now be relied upon to give an output, but there are significant ‘over-readings’, e.g. a 2017 Coriolis meter paper shows that a GVF of ≈ 5% induced a gas over-reading of ≈ 70%. These gas meters do not estimate the wet gas liquid loading, and do not have a wet gas algorithm with which to correct the over-reading if the liquid loading is known.
Industry has had more success metering wet gas flow with the Differential Pressure meter. Indeed most ‘multiphase wet gas meter’ commercial offerings have a DP meter at their core. Massed data sets from multiple wet gas test facilities and multiple DP meters from various manufacturers has been released. It shows the DP meter is significantly affected by the liquid entrainment, has significant over-reading, but crucially this wet gas reaction tends to be systematic, i.e. reproducible, and therefore describable via wet gas algorithms. ISO has published such algorithms. Nevertheless, such DP meter wet gas algorithms still require external source knowledge of the quantity of entrained liquid from an external source.
Wet gas meters are meters that output gas and liquid flowrates, with no external liquid flowrate information required. There are variations on a few generic themes. Certain DP meters can have the primary signal and permanent pressure loss DPs read, and these two signals facilitate the derivation of the gas and liquid flowrates. Other designs place two dissimilar meters in series, each with a different reproducible systematic reaction to wet gas flow, such that cross-referencing the two meters finds the gas and liquid flowrates.
More complex still are the multiphase wet gas meters. The hydrocarbon production industry often deals with wet natural gas flows where the liquid phase is a mixture of water and liquid hydrocarbon. The total gas and liquid hydrocarbon production flow is required as an asset, and the water flowrate as a disposal expense. Multiphase meters are the cutting edge of flow metering. Much of the details of various designs are commercial secrets. Nevertheless, they tend to be variations of a generic theme. Again the DP meter is at the core. Then various phase fraction devices, such as infra-red, capacitance, microwave etc. are added to decipher the phases. The central algorithm, colloquially called the ‘slip model’ as a nod to the fact the phases can travel at different average speeds, makes sense of the DP and phase fraction readings. These slip models are a semi-empirical blend of advance flow modeling and massed data sets. Any give multiphase meter’s slip model veracity continues to be a point of discussion in the metering community.
Over three decades of research, development and experience wet natural gas meter technology has gradually moved from experimental prototypes to accepted commodity products. Industry long learned the difficulty in wet gas flow metering, many obstacles needed to be overcome, not least expectation. Today industry tends to take a pragmatic view of wet natural gas metering and accepts wet natural gas meters are more complex, more expensive and less accurate than their single phase counter-parts. The various wet gas meter designs all have particular limitations dependent on the physical principles employed and the flow conditions being metered, and yet they are still in many cases indispensable. Some information is a lot better than no information. Operators must have an idea of what is flowing if they aspire to make the process as efficient and safe as possible.
The Expanding Wet Gas Metering Horizons
The net zero future looks set to facilitate a new drive for wet gas metering technologies – perhaps not in new designs but certainly in new, interesting and challenging applications. Interest and needs are coming from multiple net zero areas. For example:
At the 2023 ISO TC 193 meeting, the wet gas metering committee chaired by Kelton, received requests from Europe for the standards to discuss how to approach wet hydrogen metering when extracting stored hydrogen from wells. Meanwhile, the UK’s National Gas Transmission is initiating a program to investigate “Hydrogen & Carbon Dryness Management” – i.e. periodic wet hydrogen and wet CO2 flows are inevitable in large pipelines over time, and equipment to monitor, meter, and rectify this situation is essential. The Icelandic power company Landsvirkjun is actively testing wet steam meters to help control their geothermal fields. The CC&S practitioners are investigating CO2 metering, including gas meter diagnostic systems to identify and meter wet CO2 if and when the situation arises.
The metering of wet gas flow is essential to the energy sector and of keen interest to Kelton. Kelton chairs the ASME MFC SC19 and ISO TC193 SC3 WG2 wet gas metering committees, has staff with extensive wet gas meter experience, and offers a wet gas meter training course. Kelton is exploring how their wet gas metering expertise can support the global energy sector with its hydrocarbon and net zero eclectic wet gas metering challenges.
Richard Steven is principal measurement consultant at Kelton. Richard was the Director of the CEESI wet gas flow test facility for more than a decade, and has held positions at TUVNEL, McCrometer, TekDPro and in consultancy. Currently, Richard is active in ISO, API, AGA, and ASME flow meter standard boards. He is active in the update of the orifice meter API 14.3/ AGA 3 standard, and chairs the ISO TC 193 SC3 WG2 and ASME MFC SC19 wet gas metering committees.